Every construction project, industrial application, and manufacturing process has unique demands. While standard rubber products serve many purposes, the reality is that most professional applications require customized solutions to achieve optimal performance, safety, and longevity. Understanding when and how to specify custom rubber components can make the difference between a successful project and costly compromises.
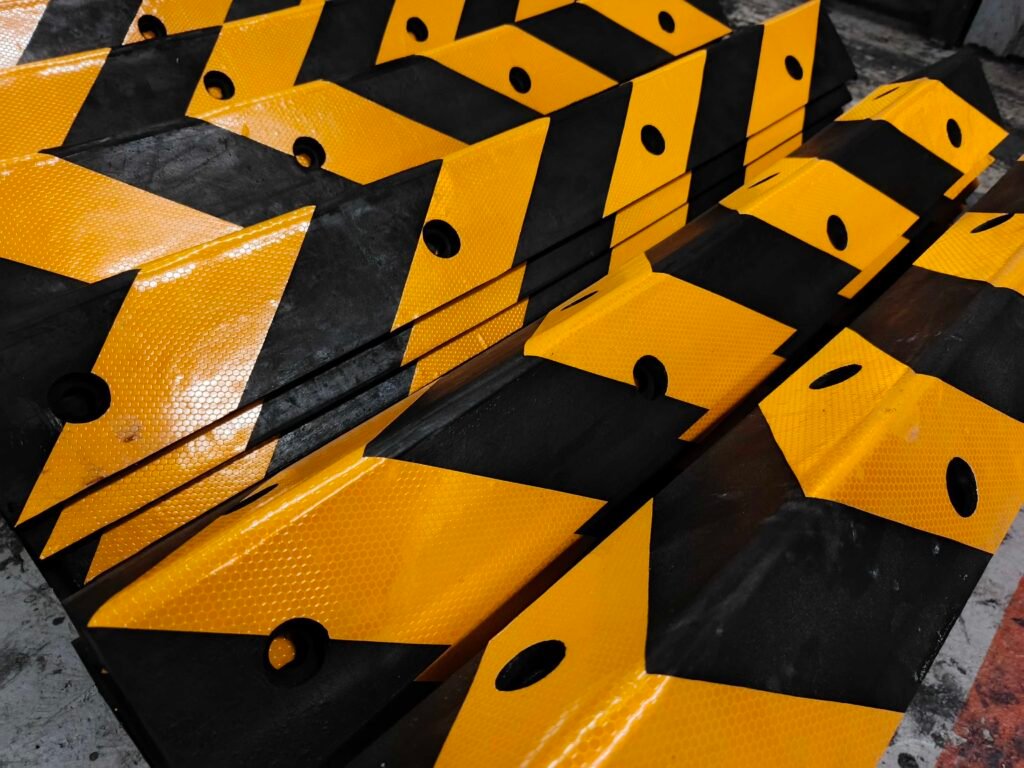
Why Construction and Industrial Applications Demand Customization
Construction projects rarely follow cookie-cutter specifications. Building dimensions vary, load requirements differ, environmental conditions change, and safety regulations evolve. A standard rubber bumper might provide basic protection, but a custom-designed bumper guard tailored to your specific loading dock height, traffic patterns, and building materials will deliver superior performance and longevity.
Consider the complexity of modern industrial operations. A standard rubber coupling might technically fit, but a custom rubber coupling designed for your specific torque requirements, operating temperature, and chemical exposure will prevent premature failure and reduce maintenance costs. The initial investment in customization pays dividends through improved reliability and reduced downtime.
Key Areas Where Custom Solutions Excel
- Dimensional Precision – Standard products come in predetermined sizes that may not align with your exact requirements. Custom rubber seal strips can be manufactured to precise measurements, ensuring perfect fit and optimal sealing performance. Whether you need a 47.5-inch rubber nosing or a uniquely shaped rubber corner wall guard, custom manufacturing eliminates the need for field modifications or compromises.
- Environmental Adaptability – Different applications face varying environmental challenges. A custom anti-vibration pad for outdoor equipment needs different compound formulation than one used in a climate-controlled facility. Custom rubber gaskets for chemical processing require specific material properties that standard products simply cannot provide.
- Load and Stress Requirements – Generic rubber mounts might support basic loads, but custom designs can incorporate specific durometer ratings, reinforcement patterns, and mounting configurations to handle your exact weight and vibration requirements. This precision engineering prevents both under-performance and over-specification.
Common Custom Applications Across Industries
- Automotive Manufacturing – Custom rubber bushings, automotive rubber parts, and specialized gaskets must meet precise tolerances and performance standards. Each vehicle model may require slightly different specifications, making customization essential for quality control and assembly efficiency.
- Construction Sites – Rubber wheel chocks need to match specific tire sizes and ground conditions. Custom rubber ramps must accommodate exact height differentials and load capacities. Standard solutions often fall short of meeting site-specific safety requirements and operational needs.
- Industrial Equipment – Custom rubber rollers and lagging are essential for conveyor systems, as belt width, load capacity, and operating conditions vary significantly between installations. A custom endless conveyor belt designed for your specific application will outperform generic alternatives in both longevity and efficiency.
- Infrastructure Protection – Rubber column guards and rubber bollards must be sized and shaped to protect specific structural elements. Custom designs ensure complete coverage and optimal impact distribution, preventing damage that generic products might not adequately address.
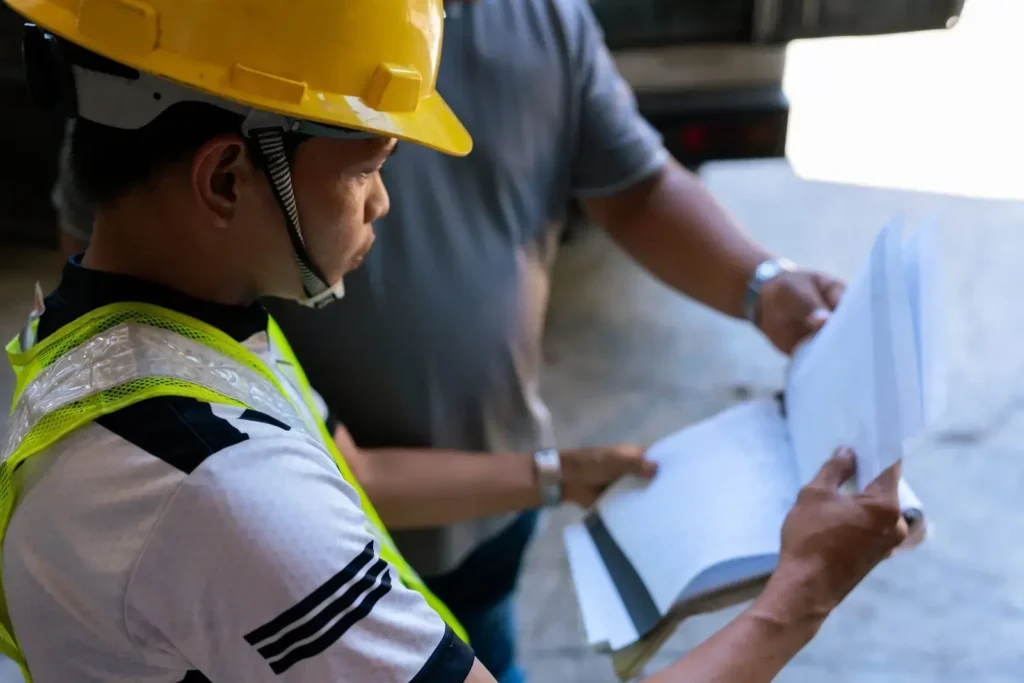
The Customization Process: From Concept to Installation
Understanding your specific requirements begins with a detailed assessment of operating conditions, performance expectations, and environmental factors. This analysis covers dimensions, load requirements, chemical exposure, temperature ranges, and safety considerations. The goal is to identify all variables that could impact rubber component performance.
Material selection follows this assessment. Different rubber compounds offer varying properties in terms of hardness, flexibility, chemical resistance, and temperature tolerance. Custom formulations can be developed when standard compounds don’t meet specific requirements, ensuring optimal performance in your unique application.
Design engineering incorporates all these factors into a component that addresses your specific needs. This might involve custom shapes, integrated mounting features, or specialized surface treatments. The design process includes consideration of installation requirements and maintenance accessibility.
Working with Custom Manufacturers
Successful custom rubber projects require clear communication of requirements, constraints, and expectations. Providing detailed specifications, including operating conditions and performance criteria, enables manufacturers to develop optimal solutions. Regular communication throughout the design and manufacturing process ensures that the final product meets all requirements.
Experienced custom manufacturers bring valuable expertise to the design process. They can suggest design improvements, recommend material alternatives, and identify potential issues before production begins. This collaborative approach often results in better solutions than initially envisioned.